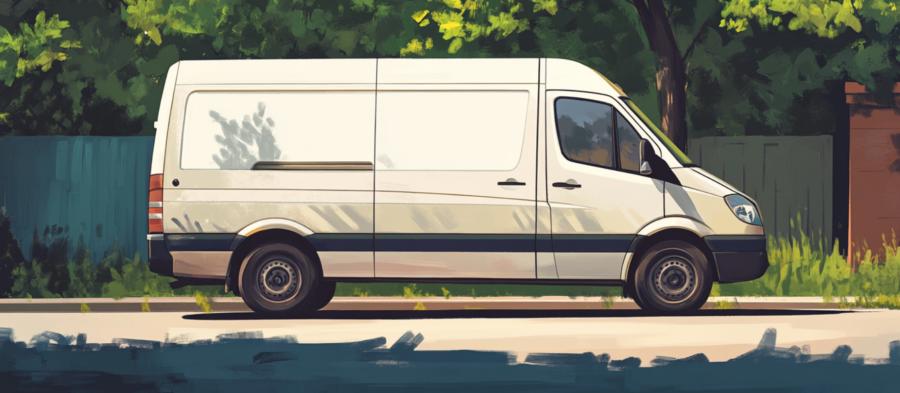
Managing a van-based business can feel like juggling with a few dozen flaming torches, especially when it comes to keeping your vans stocked and your jobs scheduled. Imagine finally reaching the job site, only to realize the one item you need is still sitting on a shelf back at HQ. Not ideal. Luckily, with the right software, managing stock and jobs becomes a whole lot easier—and way less likely to result in emergency trips back to base. Here's how to balance your mobile operations without unnecessary detours.
Get Real-Time Stock Updates to Avoid the "Whoops, Forgot That" Moment
The horror of realizing you've forgotten a crucial tool or part is universal. It's not only time-consuming but gives you that sinking feeling in your stomach. A strong software solution offers real-time stock management so you can see what's in each van before heading out. That way, if Van #3 has the very last generator part and it's closer to the site, you can dispatch that one directly rather than losing time restocking elsewhere.
Software that shows stock across multiple vans helps you redirect resources quickly. Imagine knowing exactly where every crucial item is without calling each driver and asking, "Did you grab the right cable?" With real-time updates, you can reallocate resources between vans if there's an emergency job or unexpected stock shortage. It's efficient, straightforward, and keeps drivers out of a mid-road inventory panic.
Smarter Job Scheduling by Mapping Out Each Job's Stock Needs
An efficient workday starts with an efficient schedule. When setting up jobs, smart software lets you pre-assign the necessary stock items to each task on the calendar. This way, drivers are prepped with a fully stocked van tailored to the day's lineup, and no one's stuck without a wrench on a critical job.
But let's say your scheduling wizardry goes awry, and a last-minute job pops up. With software that links stock lists to job schedules, you can check which nearby vans have the required items. No more mad dash back to the base; just reroute the nearest driver with the right supplies to the new job. It's a game-changer for companies handling high volumes of spontaneous work orders.
Handle Last-Minute Jobs Like a Pro—No Sweat, No Extra Miles
One of the most unpredictable parts of van-based operations is the last-minute job request. You know the drill: a call comes in, and suddenly there's an urgent job across town. Without the right tools on hand, this can mean a frustrating trek back to base. Instead, with software that connects scheduling and stock, you can scan van inventories and find the closest vehicle with the necessary supplies.
The result? The job gets done faster, with minimal fuel usage, and you keep your customer happy without sacrificing productivity elsewhere. Efficiency like this can be the difference between a van that's a smooth-running machine and one that's always making unplanned stops. A little bit of prep with the right software, and last-minute jobs stop being a headache.
Reducing "Back to Base" Syndrome
Frequent trips back to the base don't just waste fuel; they drain time and productivity. Each detour means lost billable hours and increased vehicle wear. Software that optimizes inventory and job scheduling minimizes these return trips by ensuring that each van's loadout is tailored to its specific tasks for the day. And if a driver's day changes suddenly, the software helps them quickly locate another nearby van with the right equipment instead of retracing their steps.
The whole idea is to keep your mobile workforce truly mobile—driving straight from one job to the next without unnecessary backtracking. It's like setting up a relay race where every handoff is perfect: no time wasted, no looking around for the baton. That's the kind of streamlined work that keeps customers happy and keeps your vans out on the road where they belong.
Smart Inventory Alerts to Avoid Surprise Shortages
Inventory alerts might not sound thrilling, but when they save you from running out of essential parts, they're nothing short of heroic. Advanced software can alert you when stock in a particular van gets low on critical items, so you can restock during routine stops instead of being caught off guard mid-job. Think of it as a heads-up before things go south.
This proactive approach helps you avoid that dreaded, "I thought we had enough!" moment. Setting custom stock thresholds for each item keeps essentials available across the fleet. You'll also have the flexibility to increase stock levels during busy seasons and adjust inventory levels based on past data. So, rather than scrambling for a backup supply, you'll already have what you need on hand.
Optimize Routes with Inventory Data to Maximize Fuel Efficiency
Fuel costs can add up quickly for any van-based operation, and aimless driving around town only makes it worse. Route optimization combined with inventory data ensures that each van takes the most efficient path to complete jobs while also accounting for inventory location. It's like giving each driver a virtual co-pilot with a full itinerary and real-time inventory updates.
This route planning also makes it easier to coordinate jobs that require shared equipment. For instance, if two vans need to use the same expensive piece of gear at different times of the day, you can plan their routes accordingly, preventing unnecessary duplicate purchases and reducing idle time. It's all about putting your resources to work smarter, not harder.
Stay Lean and Organized with Digital Inventory Management
Nobody wants their van to look like a junk drawer on wheels. But without proper stock management, that's exactly what can happen. Digital inventory management helps each driver see a precise list of what's in their van, encouraging them to keep everything in its place. This isn't just about aesthetics; an organized van means faster job completion, less fumbling around for parts, and fewer miscounts.
Drivers can digitally log when they remove or restock items, so you'll always know exactly what's in each vehicle without needing to ask for manual inventory checks. It may not spark joy quite like a tidy sock drawer, but a well-organized van is a close second.
Last Stop: Efficiency, Here We Come
When every mile counts, there's no room for wasted time or stock. Balancing job scheduling with van inventory isn't just a productivity hack; it's a way to keep your operations sharp and your customers satisfied. Whether you're streamlining routes, responding to last-minute jobs, or avoiding the dreaded "back to base" syndrome, the right software can make all the difference. Now, go ahead and give those vans the respect they deserve: fully stocked, fully scheduled, and ready to roll.
Article kindly provided by almiren.com